Quality Management
Every company is compelled to embrace the best practices approach in every aspect of its operations. Maintaining a high quality level compared to the industry standards is already a complex task, it becomes even harder to manage in a company with international operations and overseas branches, that needs to establish a constant communication channel in order to implement the same Quality levels in the processes everywhere, and to elaborate statistics and feedback from the products and services already sold to the American customers.
The cost and value of Quality
O rganizations tend to treat strategic planning and quality improvement as two separated activities. Strategic planning is usually conducted on a regular basis, using a formal structured approach. Quality improvements on the other hand tend to be very specific and targeted as a response to short term issues. The projects and areas selected for improvement should link to the broader business goals. The business goals might be lower costs, improved profitability or increased market share. The quality issues that have the biggest impact on the goals are selected for a Cost of Quality analysis, where we define prevention, appraisal and failure costs and a short term action plan to minimize them. Then it is time to generate and sustain a long term value aiming to the highest standards for the quality of your service or product, by creating a reliable system that will guide your company future quality results.
Q
uality system planning
A quality system plan plays an important role in implementing quality control systems that meet the department’s objective at optimum cost. We start in the pre-production phase, to assure quality criteria are incorporated into the product specification and documentation, such as product bill of materials, and parts drawings. We then move to the process control, providing assistance to production and manufacturing personnel, by creating training programs for workers and comprehensible work instructions. We help organizing the supervision, managerial knowledge, experience and direction to keep the the quality standards as high as requested. Finally, we implement in the quality system reviews, checks and metrics to maintain the organization focused on the quality goals. Export America can be part of your regular audits, to ensure a constant quality control over the time.
Employee involvement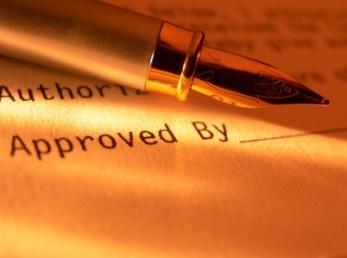
E mployee involvement is the key of our Total Quality Management approach, principles of quality managementas a system where employees are encouraged to use their expertise and knowledge to suggest methods for improvements in their work areas. These suggestions could relate to improvements in the work activity, the product, the work atmosphere or the company as a whole.
Some of the most successful companies are those that have achieved a close relationship between
workers and the managers. The policies in these companies fostered teamwork, participation,
continuous learning and flexibility; we guide your company to improve the employee empowerment, the ability to give employees the means for making important decisions, and making those decisions the “right” ones. When done right, the results are heightened productivity and a better quality of work life.